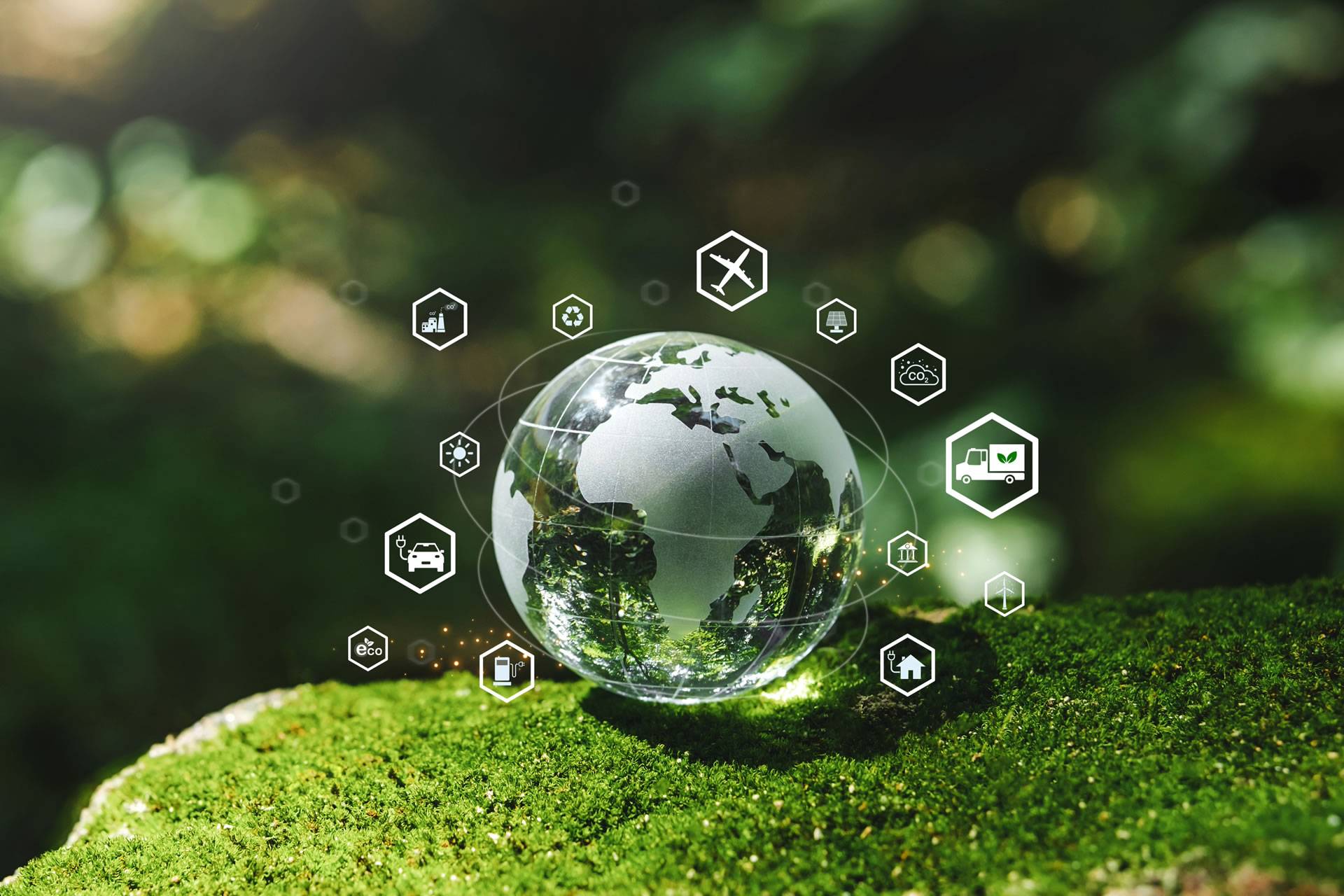
Warehousing, a critical component of the supply chain, plays a significant role in global greenhouse gas emissions. From energy consumption for lighting and climate control to transportation and material handling, warehouses contribute to businesses’ carbon footprint worldwide. However, the warehousing sector also presents significant opportunities for improvement. By implementing sustainable practices, warehouse operators can drastically reduce their environmental impact while often realizing cost savings and enhancing their brand image. This article explores best practices for reducing your carbon footprint in warehousing.
Energy Efficiency: The Core of Sustainable Warehousing
Energy consumption is a major contributor to a warehouse’s carbon footprint. Implementing energy-efficient practices is therefore paramount.
Lighting Optimization
Switching to LED lighting is a crucial first step. LEDs consume significantly less energy than traditional lighting systems and have a longer lifespan, reducing energy consumption and maintenance costs. Implementing smart lighting controls, such as motion sensors and daylight harvesting systems, can optimize energy usage by automatically adjusting lighting levels based on occupancy and available natural light.
HVAC Efficiency
Heating, ventilation, and air conditioning (HVAC) systems consume substantial energy, especially in temperature-controlled warehouses. Optimizing insulation, sealing air leaks, and implementing programmable thermostats can significantly reduce energy waste. Regular maintenance of HVAC systems is crucial for ensuring optimal performance. Consider exploring alternative cooling solutions like evaporative cooling where appropriate.
Renewable Energy Integration
Investing in renewable energy sources, such as solar panels installed on warehouse rooftops, can significantly reduce reliance on fossil fuels. Government incentives and falling prices make renewable energy increasingly accessible and financially viable.
Equipment Electrification
Replacing traditional fuel-powered forklifts and other material handling equipment with electric alternatives can drastically reduce emissions. Investing in charging infrastructure powered by renewable energy further enhances the environmental benefits. Explore opportunities for battery-swapping programs to minimize downtime.
Building Management Systems (BMS)
Implementing a BMS allows for centralized control and energy consumption monitoring across the warehouse. Based on real-time data, a BMS can optimize lighting, HVAC, and other systems, leading to significant energy savings.
Optimizing Operations for Reduced Emissions
Beyond energy efficiency, optimizing warehouse operations can significantly impact a warehouse’s carbon footprint.
Inventory Management
Efficient inventory management reduces the need for excessive storage space and minimizes unnecessary movement of goods. Implementing just-in-time inventory systems and optimizing stock levels can minimize waste and reduce transportation needs.
Warehouse Layout Optimization
A well-designed warehouse layout minimizes travel distances for material handling equipment, reducing energy consumption and operational time. Analyzing traffic flow, optimizing picking and packing processes, and strategically placing high-demand items can significantly improve efficiency.
Transportation Optimization
Transportation accounts for a significant portion of a warehouse’s carbon footprint. Optimizing delivery routes, consolidating shipments, and utilizing alternative fuel vehicles can reduce emissions. Collaborating with carriers to improve fuel efficiency and explore intermodal transportation options can further minimize environmental impact.
Waste Reduction and Recycling
Implementing a comprehensive waste management program is essential for sustainable warehousing. This includes reducing packaging waste, recycling materials such as cardboard and plastic, and composting organic waste. Partnering with recycling companies and implementing closed-loop systems can minimize waste and maximize resource recovery.
Automation and Technology
Investing in automation technologies, such as automated storage and retrieval systems (AS/RS), autonomous mobile robots (AMRs), and warehouse management systems (WMS), can improve efficiency and reduce energy consumption. These technologies can optimize processes, minimize travel distances, and improve inventory accuracy.
By implementing these best practices, warehouse operators can significantly reduce their carbon footprint, contribute to a more sustainable supply chain, and realize cost savings and other benefits. Embracing sustainability in warehousing is not only environmentally responsible but also a smart business strategy for the future.
Request a Consultation
Need more information?
Solutions